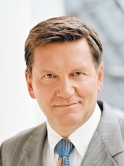
By Bjorn Fehrm
March 15, 2024, ©. Leeham News: We started the series a year ago about the New Aircraft Technologies that can be used when replacing our present single-aisle airliners.
We have covered a lot, including the typical development phases, from initial studies to preparing for the aircraft’s in-service phase.
Let’s make a resume of what we have discussed.
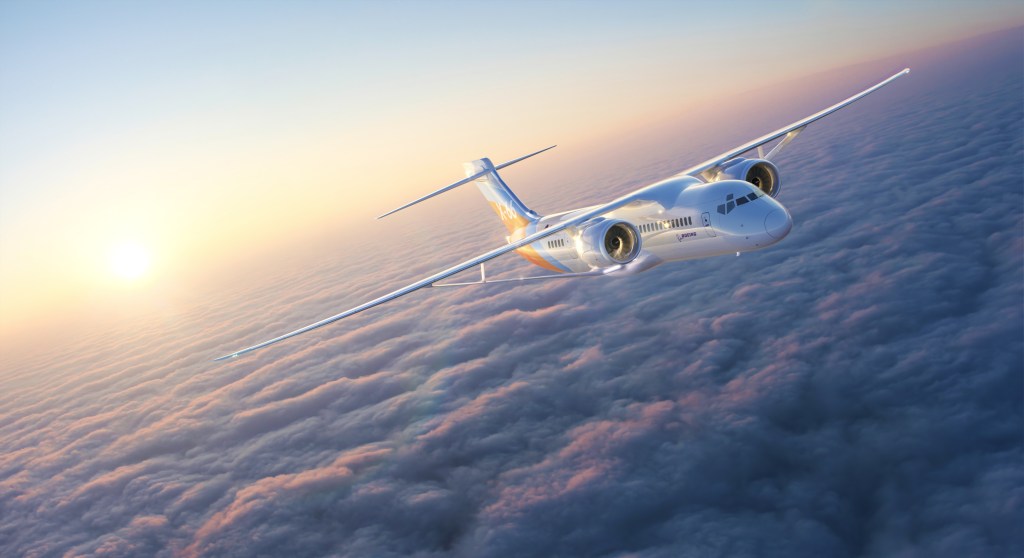
Figure 1. Boeing’s Truss Braced Wing X-66A demonstrator based on the MD-90. Source: Boeing.
New Aircraft Technologies
Over the 49 articles, we have covered a lot. Let’s run through what we looked at and learned about the ideas and technologies that can come to use for the replacement of the present single-aisle Airbus A320 and Boeing 737 MAX series:
- The first question is the airplane’s configuration. Are alternatives to the tube with wings mature enough to be considered? We must realize that the single-aisle is the backbone earner of both Airbus and Boeing. Companies will have a very low-risk appetite, as failure can risk them. In summary, we can assume that the next generation will keep the tube with wings.
- The next question is whether to keep the single-aisle configuration or if the yearly increase in passenger volumes and increasing slot constraints at key airports will favor a shorter and higher-capacity dual-aisle configuration. It all depends on the projected passenger growth. The problem is to project the movement of the heart of the market correctly over the new airliner’s 50-year lifetime.
- We then looked at the aerodynamic advancement that new aerodynamic tools, structural materials, and control techniques enable. Boeing put the folding wingtip onto airliners with the 777X. We can assume that the folding wingtip will appear on the new generation aircraft. Boeing is also exploring the next step in wider wings (to reduce the induced drag), which is the Truss-Braced Wing (TBW). The question is, will the test with a truss-braced wing on an MD-90 (Figure 1) give Boeing the confidence to dare it for the next generation? We will know by the end of the decade.
- To enable a more advanced aerodynamic shape at the lowest aircraft mass, we need materials that allow wings with advanced shapes and curvatures and strong and durable fuselages. The wing material will most likely be the classical thermoset composite, which cures chemically and is then joined with bolts (called fastened in aero-speak) into larger assemblies. The more complicated fuselage would benefit from a less workhour intensive assembly method than the bolting’s “drill and fill’. It’s where the heat-matured thermoplastic composite would allow the welding of parts into assemblies, much like car chassis parts are spot-welded into the final chassis.
- The airframe classically represents about one-third of the gain in efficiency and new engine technology two-thirds. The problem with the classical turbofan engine is the easiest efficiency improvement is to decrease the average exhaust speed of the hot gases leaving the engine (the gas overspeed versus the surrounding air), which increases the propulsive efficiency. The problem is that the method to get there, to increase the ByPass Ratio (BPR), was used heavily for the last generations, from BPR around 4 for the CFM56 generation to BPR 12 for the Pratt & Whitney GTF, an increase of three times. It will not be possible to increase the classical turbofan BPR another three times, which would be a BPR of 30+. The engine and its nacelle would be too large.
- The technology that can achieve a BPR of 30+ is the Open Rotor technology, which can achieve BPRs of double that. GE and SAFRAN propose a simplified Open Rotor for the next-generation aircraft called RISE (Revolutionary Innovation for Sustainable Engines). It puts the rotor at the front, with a non-rotating vane stage working as the de-swirler behind the single rotor. It simplifies the Open Rotor configuration without sacrificing efficiency.
- The other major efficiency improvement is found in the engine core, where new design principles and materials enable more efficient air compression, combustion, and power extraction. However, this increases the mechanical and thermal loads. It has led to the present crisis in engine durability, where airlines suffer with aircraft grounded. We will do a follow-up series about what can be done to change this situation.
We continue to Wrap our series in the next Corner.
Related
You did not mention CO2 free fuel like Hydrogen that could be a requirement for regional flights from government owned airports. The LH2 plant at airports could be a very profitable monopoly for the airport. I can think of it being connected to a pipeline system with mixed white/green hydrogen and natural gas where you separate out the H2 you want to make LH2.
Thanks for the excellent summary. We look forward to your next report on engine durability. I hope you also look into water injection during takeoff for reduced NOx, increased engine efficiency and durability (e.g. GE SPRINT.). According to several older NASA reports, water misting has the ability to reduce TIT which has an exponential positive affect on hot section life and reduced operating cost.
There were water injection in some older jet engines but there were problems besides the Munich Man United crash. It is quite popular in stationary gas turbines were you cool the combustion air and increase mass flow thru the turbines.
The Airspeed Ambassador crash at Munich might have been a simple runway overun due to slush slowing the speed during takeoff. However the plane hit a house and hut off the end of runway [Munich -Reim] which had a fuel tank inside it.
Not sure how water injection would help an air cooled radial ( with supercharger boost ) on a snowy day as used on that Airspeed ( de havilland) plane.
Neither the German or British reports mention ‘water injection’
As power weight ratios improved , turbo jets dropped the water injection
Sorry, it was another crash in Germany, Paninternational Flight 112
Thanks for that. Never heard of that one where both engines failed after takeoff as the water injection tank had a mix of water and kerosene !
Just like “perpetual motion”, emission free power sources are a misnomer. While carbon free, hydrogen will produce green house gases and whose production is water intensive – 95% of hydrogen is produced by fracking and uses an ever increasingly scarce resource – water!
see: https://www.foodandwaterwatch.org/2022/10/24/the-dirty-side-of-green-hydrogen/?gad_source=1&gclid=Cj0KCQjwhtWvBhD9ARIsAOP0GoiFp6r9c_GuyJ0UyEe8UbGpAK13Tg_SlnWuS_4RpNKnuqAgQFZH93UaAjunEALw_wcB
H2 is not Co2 free. It`s mainly won in oil refineries.
And it will probably never serve as any kind of fuel, as it`s simply to hard to handle and to reactive.
H2 brings tons of problems that are hard to solve and it`s not very efficient overall.
It might be better to remove or compensate for CO2 instead.
I think w’ll inded see higher BPR’s, lower speeds, tech stops & reduced cargo when fuel prices double..
What are the economics of higher temperatures and mechanical loads vs maintenance costs?Its become clear to me that we are wasting our time with Batteries,hydrogen and even SAF for the foreseeable future.We would be better off addressing climate change elsewhere where the tyranny of weight is less important.
Aviation is going to have to do something,so perhaps it’s better to make airlines pay more to keep their engines running.There are heaps of other marginal efficiencies possible and then we we need to get into suppressing demand and getting passengers to fund more profitable areas like insulating public buildings and more efficient power generation elsewhere.
The politicians and old industry looks for aviation to lead the technology that they then can copy. The old steel, concrete, energy, building, shipping industries are so tied to politicians and just do sporadic projects waiting for high tech and laws to show the way.
In the broad sweep of things, Boeing (if they can) will float the TBW tech (assuming its viable) along with a GTF engine.
Its exactly what they did with the 787. The airlines had not interest in the Sonic Cruiser, it was a higher pax capacity but still costly fuel burn SST.
But the Airlines did like the tech and idea of efficient. GE did a good job on the GenX and RR did a bad one on the Trent 1000, airlines have bought it in droves with a shift to the GenX as RR has never achieved the same SFC as the GenX.
The Airlines could well embrace the TBW configuration. It is familiar enough to current and there is nothing inherently wrong with the latest Gen of jet engines, its just a development issue for both LEAP and GTF. RR has more than seen the same problems with the Trent 1000, the TEN and the XWB-97 (and probably the smaller one as well but not as bad). Those are conventional turbo fan on long proven architecture.
Throw in RISE and no, airlines are not going to go with a prop.
If you need proof, just look at what Alaska Airlines has done. The Dash 8 is the ideal Turbo Prop for the Western US. High and hot is not an issue with the power. Nor is route planning a downside (you have to be able to descend to single engine performance altitude). Its a lot more efficient over a lot of city pairs in the Western US.
What did AK do? They are replacing the whole Dash 8 fleet with E-175 Jets.
So, yes they are more than willing to have lower efficiency for the sake of providing jet engine transports.
RISE is nothing more than a delaying tactic while CFM builds a new core and gets into geared systems (which the RISE has). If you read the first RISE PR and then the current, its in a constant state of morphing.
The GEnx engine in the 787 has had major sections replaced in flying aircraft- planes grounded – and upgrades on new production.
https://www.industryweek.com/operations/quality/article/21972506/ge-engines-on-boeing-dreamliners-must-be-repaired-says-faa
As GE had no engines on the A350 it hasnt had a later widebody engine comparable to the Trent XWB to compare and the GE9X, is not yet in airline service , indeed with about 5 years delay has had 10 years in development.
2016, hmmm
Not problem free, just a lot better and have gone onto put the Trent 10 into a spiral – all not wasted as the 7000 is a bleed air TEN – though you have to wonder if not an exclusive.
Do not kill the A330 yet, many have tried and today it is constantly improving and available. Some airlines don’t want Charleston built 787’s and their options are not that many. I agree it would sell better with an engine option as some airlines are not RR fans.
I wonder if there are really any airlines that would go for A330 just to avoid “Charleston built 787”. Which ones do you mean exactly?
If it would sell better – ie the real salesmen have feedback from
many potential customers- with a GE engine ( the only other choice) Im sure Airbus would do it a heartbeat.
The 747-8 GEnx engine is ‘too small’ – its a reduced power/smaller fan with lessor BPR etc.
claes:
While I am suspect on the A330NEO success, the comment was not to dismiss it.
Just that the buyers have no choice so there is no comparison between two engine mfgs. RR took the previous preference on the A330CEO by a clear majority.
I don’t think the Charleston built 787s are a real impact. If you want a 787 type, then you will buy it. Given a choice maybe not but with no choice?
Among other aspects you can’t get GE engine any other way in that aircraft class.
There clearly airlines that prefer Airbus in that general class. Less or nothing to do with the engine though it may be a bonus (or they thought it would be). Now you take what you get and that is still a Trent Ten that is resolving issues
‘Some airlines don’t want Charleston built 787’s”
The 787 new order numbers say differently
114 in 2022
301 in 2023
The A330 in all its variants has done very well, its major advantage was the wingspan of a 747-200 in a mid sized twin jet( later 747s increased by 5-8m)
In the year since you commenced this series AI has emerged as a disruptive constituent of almost all the topics you covered; when you began this series it was little more than an amusement, such is the rapidity at which this technology is evolving.
I am sure more knowledgeable folk than I could go through each of your topics and demonstrate how AI will radically impact it but consider just one topic I’m not sure you covered, FBW. Coding for such systems is notoriously laborious, time consuming and labour intensive. A properly configured AI could do in hours what a team of many, many coders would (and do) take years to accomplish.
The impact on the design and development of new types of aircraft, the compression of time and costs implied will permit new entrants into this space to challenge the incumbents. The proviso of course being, that it is not regulated out of all prospects which already it appears is the inclination.
Good comment. Perhaps more work should be put into AI for Fly By Wire (FBW) as that might become a make-or-break technology for the Truss Braced Wing (TBW) airplane. Namely, how are they going to control flutter in that long, thin, wobbly wing?
Ahh yes, the magical AI that is truly artifical.
It might even work if the programmers knew anything about what hey were writing code for.
Even students have their own ideas , so I imagine Boeing with 60 plus years or more of jet plane long thin wings have their own ideas
https://research-information.bris.ac.uk/en/studentTheses/passive-aeroelastic-control-in-truss-braced-wings-using-vibration
It is nice to see a new prototype, X-66A, with the new wing configuration. I wonder what test results are expected that can not be calculated, simulated today & verified by structural and windtunnel testing.
keesje:
I would think you would know the drill. While its all application of known aspects, its not been put into that form before.
So yea, you gotta have the confirmation that the models predict it accurately as well as wind tunnel performance was not a scaling problem.
Remember when Toyota had quality lapses in 2009-12 and was having recalls weekly? The reason was Toyota by its own admission got to smart for itself and designed the products at the time purely on CAD with little prototyping as usual. It paid dearly for that shortcut and went back to building road testing prototypes.
Reuters:
Boeing wants to build its next airplane in the ‘metaverse’
Dec 2021
“In Boeing Co’s factory of the future, immersive 3-D engineering designs will be twinned with robots that speak to each other …
It is a snapshot of an ambitious new Boeing strategy to unify sprawling design, production and airline services operations under a single digital ecosystem – in as little as two years.”
Need to find a way to funnel that half a billion $$ to BA.
The X-66A is all about wings and anti-flutter systems in real world environmet with rain, ice, bugs, dirt and smoke, anti-ice fluid of different types, wind shear, turbulence, lightning strikes, shock waves and other problems that has to be tested to see how far you can go in pushing its performance with full functioning and degraded systems. In the end of testing I would make it a fire fighter to really test its worth at Erickson Aero Tanker working together with their MD-87’s.
Very interesting wrap up:
IMO one key point to be considered is the compatibilty between high BPR engine and the wing design.
If we take the reasonnable assumption that both A and B would like to like to offer two engine OEM for their future NB because:
– first airlines would like to select “their “engine based on their own environment ( performance, MRO, warranties ,previous background with the three engine OEM,.. )
-and at least as important for A and B minimize the engine risk ( see GTF current issue)
TBW high wing looks very promising because its geometrical compatibility with both advanced GTF/futur downscaled Ultrafan and RISE open rotor
by comparison with A320 “low wing” style. In other words open rotor need a more specific wing design ( gull wing to increase ground clearance?) which may be not optimized with gear engines with nacelle.
GE/Safran should be very cautious in their RISE approach except if A or B does not follow this basic assumption . I am sure they are aware because their RISE “single approach” is risky from an airframe design point of view for this reason and also some big passenger market like US ( see above @TW comment I share) does’nt like ” prop” engine .
Keeping in mind a Dash 8 is faster on some shorter routes and almost as fast on longer routes (and has the option to max the throttles to make up time)
And still they are being phased out in the US and not big sales anywhere in the world.
ATR that has the market to itself selling 60 a year and there has been a downward trend.