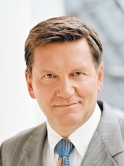
By Bjorn Fehrm
June 14, 2024, ©. Leeham News: We do an article series about engine development. The aim is to understand why engine development now has longer timelines than airframe development and carries larger risks of product maturity problems.
To understand why engine development has become a challenging task, we need to understand engine fundamentals and the technologies used for these fundamentals.
We have covered the main thrust-generating device, which we can call a propeller, fan, or open rotor, depending on the application. To drive the main thrust device, we need a lot of shaft power, which is provided by the core. We start with how the core, which is a gas turbine, generates power.
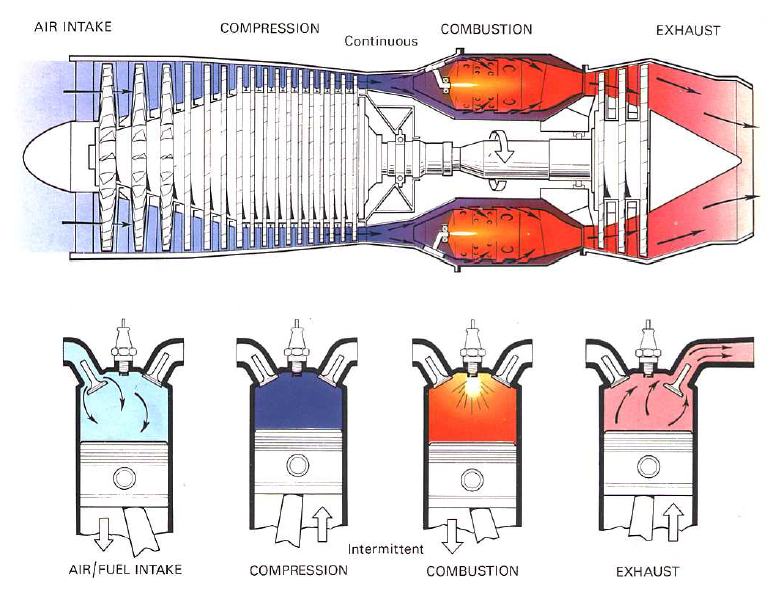
Figure 1. The core cycle compared to a piston engine cycle. Source: Rolls-Royce, The Jet Engine.
How air pressure, volume, and temperature are connected
To understand what happens in a gas turbine, we need to understand some fundamentals about air. Air is made of a cocktail of gases that reacts to changes in one property, like volume, with changes in the other properties, pressure and temperature.
The relationship is: Pressure * Volume = a constant * Temperature
We only need to know that if we increase the pressure at a constant volume, the temperature will increase. Or if we increase the temperature at constant pressure, the volume will increase. And so on.
The core is a gas turbine
Figure 1 shows a jet engine cycle compared with a piston engine cycle. Jet engines were the first, simplest aircraft gas turbine engines. A jet engine and a turbofan differ in that the first compressor stage is larger for a turbofan, with a larger diameter, Figure 2. The first stage, now called a fan, pushes accelerated air both into the bypass channel and the core.
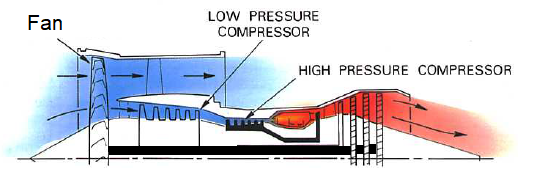
Figure 2. A two shaft turbofan engine. Source: Rolls-Royce, The Jet Engine.
In figure 1 we have a single shaft gas turbine core, in Figure 2, a two shaft core. There are also three shaft engines from Rolls-Royce and Ivchenko. We will come to why engine makers use several shafts in their engines.
The gas turbine cycle
We use Figure 1 as the example of a gas turbine as Rolls-Royce has made a nice complementing graphic (Figure 3), which we can use to explain what happens in a gas turbine.
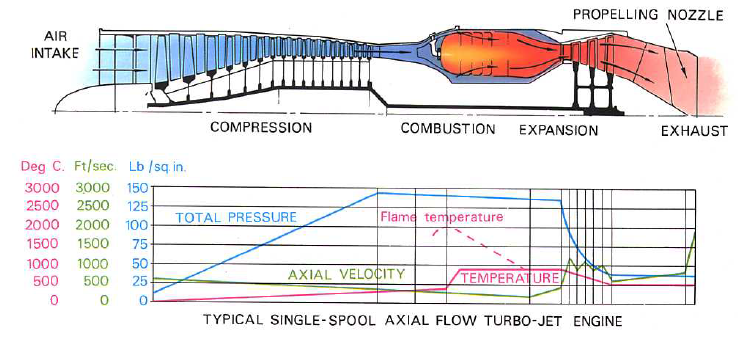
Figure 3. The gas turbine cycle. Source: Rolls-Royce, The Jet Engine.
A car piston engine and a gas turbine engine are both heat engines. It means they generate power by heating air to increase its energy and then extract work from the heated air.
They both have;
- An air intake. In the classical piston engine, the air is mixed with the fuel in the air intake. Advanced piston engines, like the gas turbine, have fuel injection at the start of the combustion phase (direct injection engines).
- The air is compressed to make the subsequent combustion more efficient. Figure 3 shows the compression in a multistage axial compressor, with the pressure in PSI in blue. The ambient air at the intake is at 15 PSI (1013 hPa), with the final pressure at the end of the compressor 10 times higher. The compressor has a Pressure Ratio (PR) of 10. The higher the compression, the higher the combustion efficiency. A PR of 10 is low, typical of engines from the 1960s. Today’s engines have PR 40 to 60. Compression increases the temperature of the air, starting at 15° C and ending at around 400°C.
- The combustion in a piston engine is in a constrained volume, thus the pressure increases, which pushes the piston down. The combustion in a gas turbine is not constrained in volume, the combustion gas can expand towards the turbine (the compressor, which has ~150 PSI at the end, is a less attrative way for the combustion gases). The combustion under constant pressure (it declines slightly due to flow losses in the combustor) makes the gas turbine a Brayton heat engine, where the combustion is done under constant pressure and expanding volume. The 400°C at the end of the compressor has now increased to close to 1,000°C. This is a low value today, where the latest, most advanced engines almost double this value.
- The turbine stages take the expanding gas and give it a high velocity in the first static stage of the turbine, called the turbine nozzle. The high-temperature, high-velocity combustion gas now generates shaft power in the turbine stages. Finally, the jet exhaust nozzle of the gas turbine uses the remaining energy of the gases to accelerate the gas mass flow to a suitable exhaust speed, generating jet thrust. The jet thrust is 100% of the thrust for a jet engine, about 10-20% for a turbofan, and less than 10% for a turboprop or open fan engine.
We will go through the different stages of the gas turbine and analyze why it’s such a challenge for engine OEMs to make the engine and its core both reliable (running 99.9% of the time when properly cared for) and durable (staying on the wing for a lot of flights).
Related
A small comment, the air is compressed to increase the amount of work that can be transferred in the turbines after combustion, all fuel can be burned efficiently no matter the pressure (like in a house heater just giving heat and no work), the main difficulty is compression at high efficiency and handle the transients, the hotter you burn the more work you can get from the turbines. The hotter the air in the compressor the less efficient compression hence ideally you want to cool the compressor air inside the compressor and pump the heat back into the burner before fuel injection. Today a big portion of the compressed air is used for cooling the flame and turbine components, could you avoid that cooling and burn the fuel stochiometric you would gain performance. In theory that is possible with ceramic turbine blades/vanes and discs. In a high efficiency turbine the LP turbine exit temperature is less than the compressor exit temperature, so if you want to use it to reduce fuel consumption you need a heat pump.
outstanding!
The turbine stage does not take the expanding gas and give it a higher velocity. The turbine slows down the flow as it extracts energy to turn the compressor.
Not quite. A turbine stage is defined as the combination of the static part and the rotating part.
I wrote the turbine stages, which include the fixed static vanes, which change the direction and velocity of the flow. As I write, the first static vane, called the turbine nozzle, changes direction and increases the velocity of the flow for it to hit the first turbine stage blades at an optimum Angle of Attack (AoA) and, depending on the turbine type, to slow it down. We will cover all this in detail in the series.
Yes, the amount of action and reaction designed into the turbine blade. Simplified change of direction vs change of momentum.
I’m trying to absorb this as much as possible and I very much appreciate this informative free content.
Off topic I know (or extremely tangential), does the forward and high positioning of the 737MAX engines have a similar effect with yaw as it does in pitch?
It can be dependent on speed and yaw angle if the fwd body can shadows the nacelle. A bit like the wing shadow the horizontal T-tail and the need for stick pusher.
A little Boeing pricing info:
(Sorry – I know that this is not about the topic, if is however, the most recent open thread and relevant to the profitability of aircraft and engine OEM’s)
There was an analysis of the BA orders and deliveries on a financial website:
https://seekingalpha.com/article/4700095-boeing-in-crisis-airplane-orders-deliveries-tumble-stock-falls?source=content_type%3Areact%7Csection%3Asummary%7Csection_asset%3Aall_analysis%7Cfirst_level_url%3Asymbol%7Cbutton%3ATitle%7Clock_status%3ANo%7Cline%3A1
The relevant part:
‘In May, Boeing logged four gross orders, all of which were for wide body airplanes with a value of $637.6 million with EVA Air being the sole customer with an order for four Boeing 787-10 airplanes.’
Based on that information, BA received ~$160 million per 787-10.
‘During the month, the plane maker saw Aerolineas Argentinas cancel an order for one Boeing 737 MAX (8)…With four gross orders and one cancellations, the net order tally for the month was just three units with a net order value of $585 million.’
$637.6 -$585= $52 million for the Max 8 from AA.