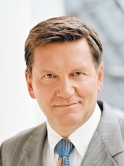
By Bjorn Fehrm, Henry Tam, and Andrew Telesca.
November 26, 2021, ©. Leeham News: Last week, we started our analysis of the serial production phase. If development is filled with revelations and problems to solve, production has it as well.
We start this week by looking at the beginning of serial production, where several issues are overhangs from development. There are areas of the aircraft, though we have achieved our Type Certificate, that are not quite to the maturity level we want for long-term serial production.
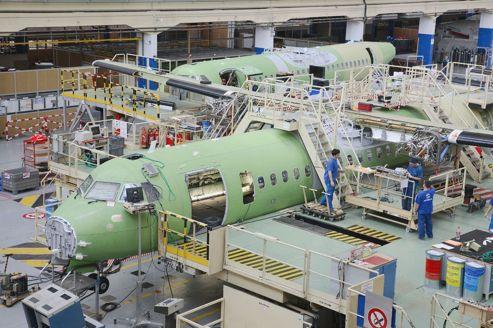
Figure 1. A typical aircraft Final Assembly Line (FAL) site. Source: ATR.
Early Production
Serial production is typically started before the end of development and before the design Type Certificate has been earned. This means we have parts in the aircraft that are not fully mature and we fight with:
Logistics & Coordination Issues:
- Parts and systems that are not to final specification, or the wrong revision for the aircraft
- Late arrival of parts that are difficult to produce for one reason or another
- The introduction of customer delivery reviews may introduce the need for changes and reworks that we as the OEM accept. We could also run into contractual disputes (especially if the program was delayed) that can slow deliveries and increase production costs as the aircraft for this order might be taken off the line and parked until we know how the dispute is resolved.
Design Variation and Optimization:
- Parts and systems that are overweight create variant problems. The first aircraft in a new program are typically 5% overweight compared to what our preliminary design put down. Aircraft development and production is a constant fight against weight creep, a fight that never stops. As we go into production many small changes will be introduced to try and correct this. Gradually the product reaches a mature state regarding revisions on parts and systems and their final weight.
- We will need to produce the variants sold to different customers. Each customer has a slightly different specification of the aircraft, especially in the cabin. Such first aircraft to a slightly different specification are called “heads of versions”, and these require extra work to get the revised parts to fit and our assembly team to get comfortable with the new parts. A changed specification means options management and certification, the introduction of new interior bits, and validation of the design with original or new foreign authorities who may require design changes or where delays for inspections could cause hiccups in the delivery process.
Slow Defect Resolution:
- Parts and systems that need extra work consume more work hours to complete, and therefore cost more than planned. If we find structural parts that are not to specification, the best line of action might be a repair of the part instead of rejection and production (and therefore wait) for a new part. Such repairs will take longer as our repair manuals may not be completed. It then involves intense dialogs with engineering to understand what can be done and how. A “use as is” dispositions may not be possible as we don’t have the data to support the variance of the part, and we might have to wait and see if the defect is common enough to warrant the additional engineering effort to investigate a corrective repair. As we wait, it means a higher rate of expensive “remove and replace” dispositions.
- Traveled work packages are fitted to the aircraft out of position, something that costs extra. This can be a result of late arrival or not to spec parts. Traveled work means the final state of an area like an air duct or cabin fitting will only be installed once the aircraft has rolled off the FAL. This keeps the production line moving, but if the volume is too large it pushes the bottleneck to our delivery center, where the work is often less efficient (more costly) to perform.
- Early aircraft are more likely to discover issues during their production flight tests after the FAL process. It will increase our bucket of out of sequence work.
- Certain problems might be too complex to find an immediate solution to. We can then have an agreement with the customers that certain functionality will be fitted after delivery and entry into service, via a modification kit. An example is how Boeing agreed that the vertical tail tank for the 747-8 was not usable initially until its full influence on the aircraft was cleared in flight testing. A modification was defined (it can be as simple as a paper change or just a software update for the systems involved) which was installed on the aircraft after it had entered service.
The reasons for the learning curve
The initial high cost of the first aircraft is because of all the above problems. But it also comes from the time it takes for assembly mechanics to confer with designers how it all is intended to come together. Parts that run into tolerance conflicts will not fit and need adjustments. The need for adjustments must be reported back to design and production engineers so that the procedure for deficiency correction can be verified. “Is it OK if we machine this surface a further 0.2mm to make the part fit?”. This can only engineering answer as it has the stress calculations and fit principle for the part in its design data.
Often the designers/product engineers/planners come to production to physically see the problems. Each problem area is thoroughly discussed. A fix is devices and is tried in subsequent aircraft.
When a production chain runs into problems with parts, it tries to continue without the part or fit it provisionally while waiting for a part that fills the specification. This means this area of the aircraft must be opened again (if it was behind something) and the final part put in place.
All this cost time and time is paid work-hours. If one analyses a simple area like an aluminum structure for example the horizontal tail, one can see that the cost of production has almost no relation to the cost of the aluminum alloy used. The all dominant cost item of the horizontal tail is the amount of work and machine hours that the item has consumed in its production.
The extra work hours spent in making different sections of the aircraft is, therefore, later found in the company’s “time used for this aircraft serial number” reports and finally in Cost of Goods Sold, COGS.
The initial part of the production is struggling with a very large consumption of work-hours to handle all the disturbances in the production. Late deliveries mean flying in parts that should have arrived with normal transport, and purchasers and production planners literally carry certain items to the production site.
As production settles down, items fit and the specification of the 500,000 items in our aircraft reach their mature and stable state. It’s when normality arrives and by it, lower costs.
Related
Interesting!
I am confused regarding the overweight thing. How does this happen? 5% is quite a lot.
Hi Walter,
in drips and drabs. As said, an aircraft this size has 500,000 components, many of these new designs for this aircraft. All these have design goals where several are weight (mass really). It’s always difficult to reach such targets and in aircraft projects (bin there myself) several systems and components come to the assembly not reaching these targets.
Aircraft projects have weight campaigns to combat this, several during an aircraft program’s run. Gradually you reach a level of diminishing return. That’s when you stop and accept where you are, seldom at the level of the target from preliminary design.
Thanks for your explanation. Still in the design documentation the parts should have precise dimensions and therefore mass specifications. So what exactly happens when you cut weight during the production of the first batch of aircrafts? Are the first exemplars for example produced with higher tolerances that are subsequently toned down to what is specified in the design documentation?
As ground tests of the static airframe and flight test data are collected the actual stress levels in many components are revealed compared with assumed or generated levels with stress analysis applications.
It gives an opportunity to reduce material dimensions on non-mating surfaces. You can see on most aeronautical parts that it has a lightweight design with hollowing out or holes where possible. This is taken to a higher level once you have more solid data.
So there is some kind of “post preseries redesign” using test data, makes sense.
There is also redesign based on readiness goal time Constraints.
I.e. some part may be suboptimal but it is _ready, available_
Remember that “overweight” is a relative term. The performance targets that are developed at the outset assume that the empty weight will be X before the detailed design has even begun.
As the detailed design progresses, a new empty weight Y might be calculated which becomes the basis for performance (range, takeoff, landing, block fuel, etc) and payload guarantees.
Y can be substantially different from X if some of the original assumptions turn out to have been wrong and you can also get into a feedback loop of sorts if a heavier than expected airframe needs a bigger engine to meet performance goals, for example.
Once Y becomes the target weight, you can still have unrealized risks (stuff for which detailed design is not finalized) and opportunities (stuff for which detailed design can be further refined to reduce weight) up until the time that the configuration is frozen / matures.
You often have requirements creep, where Customer inputs are accepted but it causes increased mass and cost, it might be more common on military Aircrafts where the customer can order and pay without really upsetting its shareholders of delays and increased cost. Sometimes the Aircraft manufaturer does not fully understand the risk of implemeting Customer wishes (like Saab 2000 and Crossair). It used to be that everthing that broke were beefed up and part count kept increasing. You get shipments that are over weight and late what do you do now not having moitored your suppliers every step and stop them as soon as a deviation is discovered.
Bjorn. Very Good Work Here.
The raw materials themselves make a huge difference in the vehicle weight. Composite Prepreg material has a resin content spec window. It must be between X and Y percentage. Resin is very heavy compared to the fabric. The risks of being below the resin content minimums are far more severe than being above the tolerance zone. “Dry” parts are almost universally rejected for structural reasons. Wet parts are frowned on, but structurally ok in most cases. The prepreg manufacturers know this and always make their product towards the upper range of resin content. This means it will always be heavier than nominal but perfectly acceptable. The same gos for aluminum sheet, it’s always at nominal thickness or above for the same reasons. Sealants are also another place where it easy to gain weight. The majority of sealant is hand applied and having a tiny bit extra makes the process so much easier for the applicator. Tens of thousands of little bits is quite heavy. There is also the matter of secondary structure fastener length. All those screws holding wire bundles inside clamps, the wiring termination fasteners all the screws holding access panels on, tie wrap ends, literally millions of things might be 1 grip length too long. It meets spec but is unnecessarily heavy because not only is the fastener longer, but an extra washer is probably needed.
Weight gain is a death by a thousand cuts and a little bit of inattention to detail tens of thousands of times adds up.
Long ago we had a weight bounty of $3200 per pound of weight savings. We would pay that much to engineer weight reductions.
Interesting, thank you for the explanation.
$6.4M per ton. I think most OEMs would take take that!
Thanks, Scott, an excellent contribution from someone who knows!
Another question is, if the OE knows how tollerance and acceptance criteria work too. Why don’t they include them in weight specifications? Commercial is a factor there I guess. Getting OEW’s to be become public on new aircraft always takes some time. But often MTOW bumps during development tell the story, payload has to remain intact..
Bjorn:
Correct me if I am wrong but are there not issues with the Tier suppliers that engineer their portion of the parts ? (weight issue in this case)
Boeing no longer designs the aircraft (in case of 787 major parts) but sends out specs if I understand it (and on the 787 there was no monitoring of that until it hit the assembly hall). Maybe a simplification?
As a tier supplier/engineer you would tend to over than under (most cases, lets not talk about 787 battery!)
Flip side if I have it correct was takign weight out led to the wing join issue on the 787-8. Seemed to be a fairly rare case of overestimate of the structural capability in that area.
At the core : (sufficient coverage) Interfae definitions.
Airbus needed those to be perfect from day one ( compromise on the a380)
Boeing used to fudge it ..
They hadn’t made an all composite airliner before so they had no experience of what the various sub assemblies would weigh. The decades of accumulated experience with aluminium parts and the estimates that experience gave them weren’t of any use for 50% by weight that wasnt composite
[2005]https://www.compositesworld.com/articles/boeing-sets-pace-for-composite-usage-in-large-civil-aircraft
Duke:
Clearly they did have a good idea what it should weigh and they then took enough weight out of the 787-9 to meet the original specs.
Also clearly they did not have any handle on the sub contractors until after the empty rollout and things got sticky and they formed the teams to deal with that.
Apropos: “side of body join”
This actually was a case of “too stiff”
And a properties discontinuity over the join.
Two comments :
“vertical tail tank for the 747-8 ” : I would say “horizontal tail tank initially deactivated due to flutter”
overweight issue due to airline requirements : Few years ago , there were two different kinds of “customer “equipments in option : BFE ( buyer furnished equipment) for which weight spec are under customer responsability and SFE ( supplier furnished equipment) where impact on final contractual OEW is under OEW responsability . I don’t know if this distinction is still valid?