By Bjorn Fehrm
Subscription required
Introduction
June 6, 2016, ©. Leeham Co: In January last year I had a discussion with Airbus CEO Fabrice Bregier regarding the innovation level at Airbus. The background to the discussion was that Airbus was trailing its direct competitor, Boeing Commercial Airplanes, in innovations since the early 2000s.
Airbus started life as a more innovative company than Boeing. It was using new technology in an aggressive way to gain product advantages on the incumbent Boeing. Examples are the universal use of Fly-By-Wire (FBW) and the standardization on a common cockpit layout for all its aircraft, whether single or dual aisle, Figure 1.
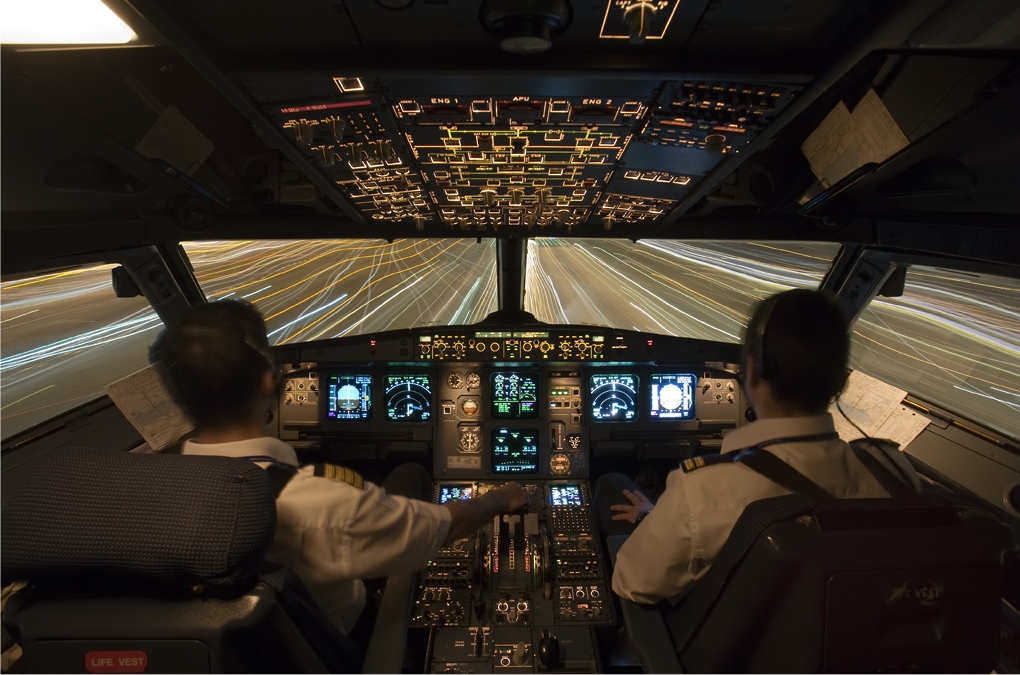
Figure 1, Airbus A320 cockpit laying the ground for a common cockpit standard. Source: Wikipedia.
The FBW and common cockpit enabled customer pilots to cover a wider range of aircraft with minimal training. Airbus also led the aerodynamic development with high aspect ratio wings for its A320 and A330/340 series aircraft.
Somewhere during the problems with the A380, the creative and innovative spirit got caught in the aim to unify the group, to make sure that the “I make it my way” initiatives stopped in the different national industries that made up Airbus.