Redefining the 757 replacement: Requirement for the 225/5000 Sector, Part 6.
By Bjorn Fehrm
Subscription required
Introduction
18 March 2015, c. Leeham Co: In Part 1 of of this series we investigated the market sector 225/5000, which is our name for the market segment beyond the capacity of single aisles A320 and 737 aircraft. Boeing calls this Middle Of the Market, MOM, and is studying which aircraft type would best cover this segment.
In Part 5 of the series we concluded that beyond 220 seats a dual aisle aircraft can be competitive as it can increase utilization due to shorter ground turn-around time. We now conclude the investigation by looking at what Airbus response can be based on a further developed A320 and how it would stack up against optimized seven abreast dual aisle alternatives from Boeing's MOM study, one of these using Boeing's patented elliptical fuselage, Figure 1.
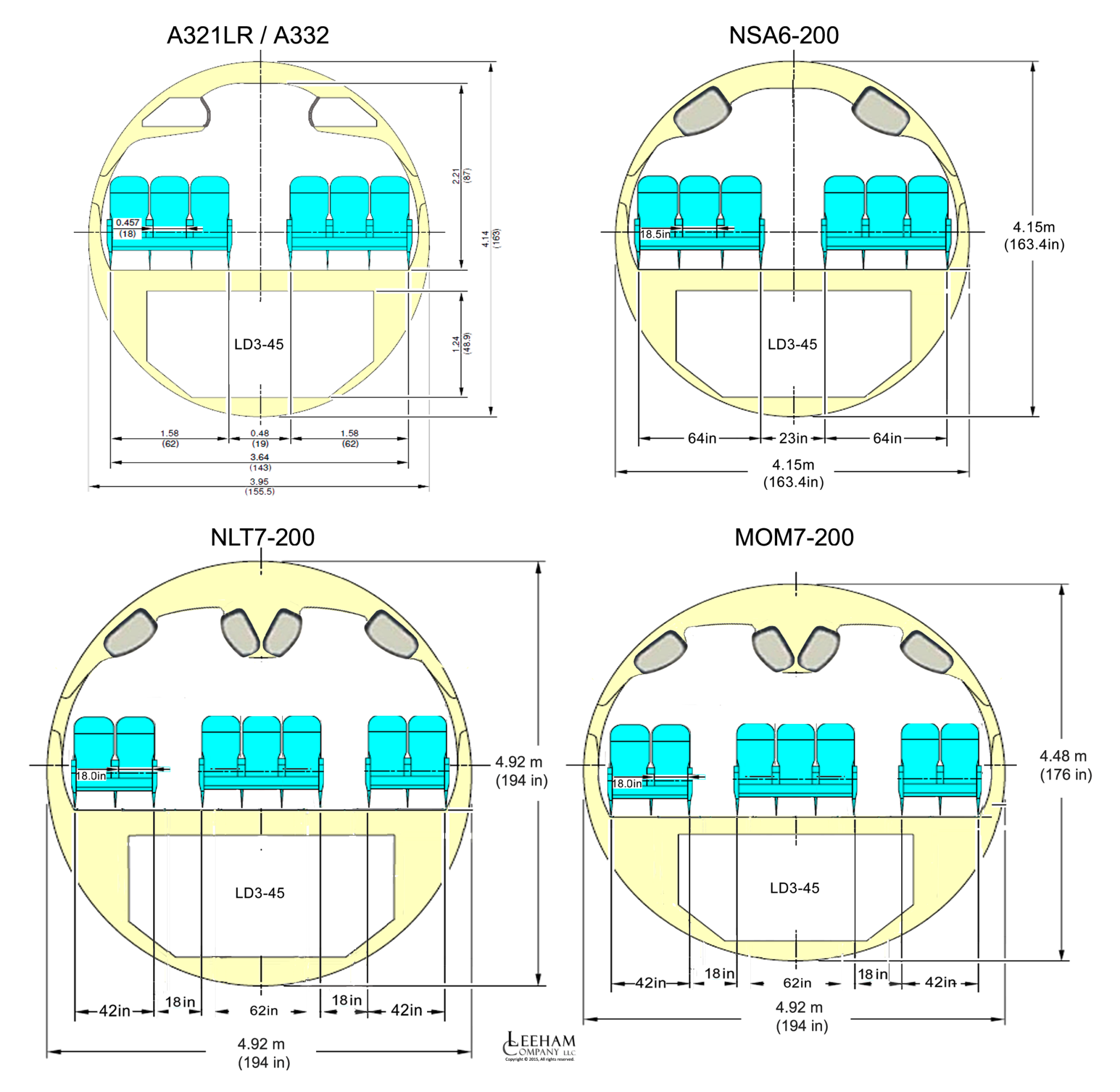
Figure 1. Compared cross sections for MOM market. Source: Leeham Co.
Summary
- The rational further stretch of Airbus A321LR is a re-winged/re-engined A322 with 30-40 more passengers, or five to seven additional rows.
- We compare this development with optimized models from our MOM studies and the A321LR.
- For the comparison we focus on efficiency in weight, drag and fuel for the different alternatives. How competitive will a stretched A321 be and how close in weight and drag comes an elliptical MOM model?
To read the rest of the article Login or Subscribe today.
Category: Airbus, Airlines, Boeing, EADS, Future aircraft, Premium
Tags: 737/757 replacement, 757, A320NEO, A321NEO, A321neo Long Range, A321neoLR, Airbus, Boeing