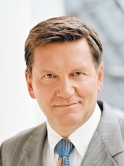
By Bjorn Fehrm, Henry Tam, and Andrew Telesca.
October 29, 2021, ©. Leeham News: Last week, we looked into Instructions for Continued Airworthiness (ICAs), and what roles it plays in air safety.
Equally important for air safety is the qualification and training programs we design for the organizations and people that shall carry out the work with our Instructions for Continued Airworthiness.
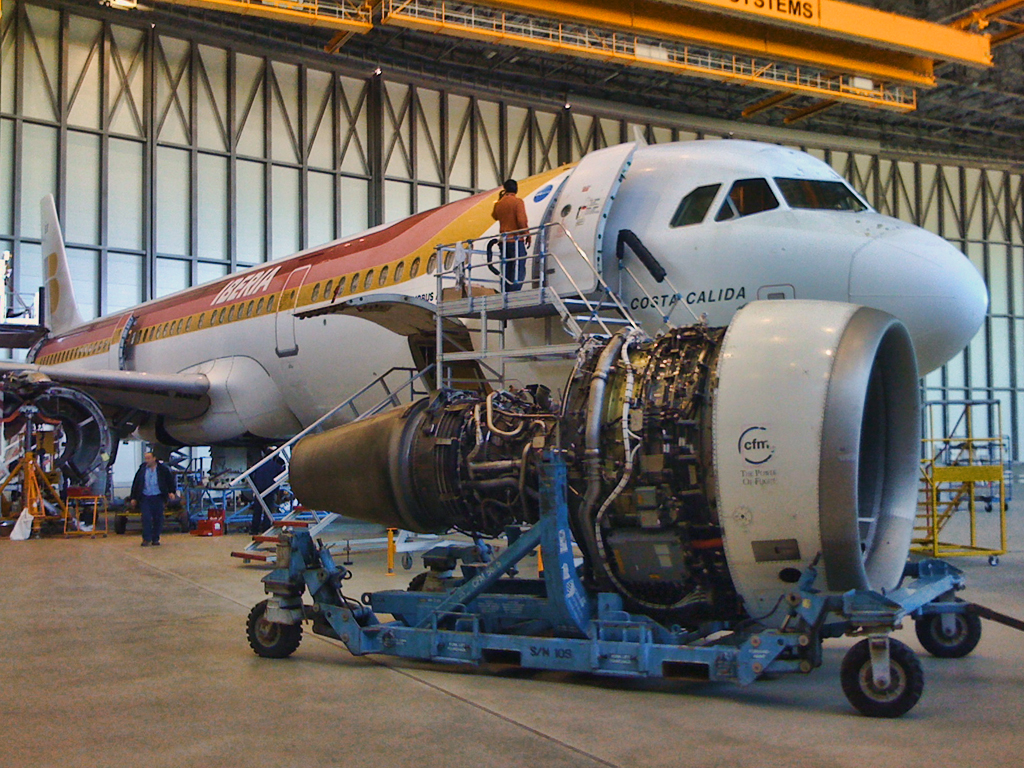
Figure 1. Aircraft Maintenance on an IBERIA A320. Source: Wikipedia.
Qualification and training for organizations doing Continued Airworthiness work
It’s not enough for us as an OEM to make documents and instructions for Continued Airworthiness we must also design a program for how to qualify and train the different organizations that shall carry out the work according to the Instructions for Continued Airworthiness. Our customers will likely want this training to start in advance of first delivery in order to ensure a smooth entry into service. This is often carried out as we train the airline’s trainer.
When the first aircraft start their operation we must make sure:
- That the airline’s mechanics can do the line maintenance needed. Typically this is organized as a daily check and a weekly check. The daily check goes through the cabin and checks that all seats and seat belts are ok, that all the emergency equipment is there, and in the aircraft logs that no BIT self-tests failed yesterday or other problems were noted. Then outside, that oil, fluid, battery, and useable water levels are ok, and the wear of the tires and brakes are within limits. The Weekly check adds tasks such as deeper inspections in the cabin, such that seat belts and foldable tables are ok, lavatory checks, etc. There are also inspections behind certain hatches and certain system self-tests are done to get conditions status.
- That the organization (often the airline but also specialized Maintenance and Repair Organizations, MROs) that does the regular Base checks (often called A, C, D checks) have the qualification to do their work. It’s called Base checks because typically the aircraft is towed from the flight line into a hangar to do the work. The interval between the simplest check, the A check, is now the base interval for our maintenance cycle. Let’s say the Maintenance Review Board agrees that we can start the Base check at 500 Flight Cycles (FC) and 400 Flight Hour (FH) intervals.
For the early part of the aircraft’s lifecycle, the airline needs to then schedule that the aircraft shall be put in a hangar before 500FC/400FH and the task that has these limits are carried out. Typically this simple check takes two to three mechanics a week to perform on a larger turboprop. For our 19 seater, we could need one mechanic for a week. Our maintenance training and qualification program and personnel must be able to train and certify the mechanics that carry out this work. In the early days, we will likely want our personnel on-site to support the customer when first performing these checks.
- The maintenance cycle performs this check each time the aircraft reaches the 400FH/F500FC limits. At a typical initial limit of 2500FC/2000FH (about five to six times the A check interval), heavier checks often called the C checks are needed. Now parts of the cabin are removed so that structural inspections can be done behind sidewalls and galleys/lavatories. These form part of a Structural Inspection and Corrosion Prevention program that we have to design and train MROs for. Aluminum corrodes, especially below lavatories, and there are inspections and corrosion fluid application necessary in sensitive places. The initial C checks require perhaps 200 Workhours and take two to three weeks to complete. As the second, third, fourth, etc C checks are due, additional tasks are added, and the work content increases.
- The C checks are often also where Service Bulletins (SBs) and ADs are carried out, which can be minor or larger modifications to the aircraft so that its longer-term airworthiness is maintained. For each SB, AD, or other modification of the aircraft, we must produce complete documentation and training/qualifications. We may also have to work with the customers to modify the SB/AD if there are customizations (or even just build to build variations) that prevent its direct incorporation on their airplanes, which could require seeking an Alternatives Means of Compliance (AMOC) from the regulator. The Air Astana E-190 incident mentioned below was caused by an unclear SB change that made the wiring of the ailerons difficult to do correctly.
- During the daily operation and at the A and C checks, failed, timed, or on condition system items are removed and sent in a repair loop. The maintenance organizations that carry out such re-condition/repair must have adequate documentation, training, and qualification for doing this work. The Boeing 737 MAX crisis was triggered by a failure to carry out the maintenance of an Angle of Attack (AoA) vane correctly by a repair company. The vane output was offset from its datum and it wasn’t discovered by the final check in the company. The line repair mechanic that installed the vane didn’t check its installed output according to the ICA. These failures contributed to the death of 346 people.
- As the aircraft approach somewhere around 15,000 to 20,000 cycles the C-checks change to what is called heavy checks or D-checks. Now the complete interior is removed and the whole aircraft is inspected for fatigue signs. This takes months and it’s a significant cost to an operator.
- We, as the OEM, are responsible that the documentation and training for all the levels of maintenance for our aircraft have been done, to transfer the necessary competence to our customers so they can do a correct job. We can’t produce all this material and training. Our suppliers must do their part for their system/parts and that they propose repair/recondition organizations they have trained and qualified for this work. Our responsibility is to legally bind the suppliers to their responsibility and to do the necessary verification that what they propose fulfills the requirements.
There are numerous examples where faulty performed maintenance has been the cause of accidents (click on the headlines to get to the link):
American Airlines Flight 191
Incorrect mounting procedures for the engine and pylon cause the DC-10 to lose the left engine, nacelle, and pylon on takeoff. The separation tore off 3m of the leading edge in the process, damaging the hydraulics to the slats so these retracted. The aircraft stalled over the slat-less wing and crashed in May 1979.
Alaska Airlines Flight 261
Inadequate lubrication and faulty final check for wear of the horizontal tailplane trim jackscrew during C-checks had it fail completely during flight and send the MD-83 pitch down into the water in January 2000.
Air Astana E-190
Unclear maintenance instructions led to an accidental reversion of aileron control cables during maintenance, which led to a near crash in November 2018.
American Airlines
This article from yesterday describes how American Airlines did not act upon their Instructions for Continued Airworthiness (ICAs) issues correctly.
Related
Bjorn:
I think this is wrongly worded. Agreed that cables are known as wire rope, but in this case I would say the control cables were run incorrectly. If I have it right the ailerons were control cables and the spoilers were FBW.
“The Air Astana E-190 incident mentioned below was caused by an unclear SB change that made the wiring of the ailerons difficult to do correctly. ”
The fact they recovered from that and made any landing was a testimony to maintain your cool under the most bizarre conditions.
Since we are this week overwhelmed by the rhetoric of COP 26 now would be a good time to show why your new 19 seat TP of the future would never reach this stage.
The author would do well to acquaint himself with such phrases as “Principles for Responsible Investment” & “Equator Principles”and others that come under the auspices of ESG and are concomitant with institutional investments in new industrial products or projects. In the same way as credit rating agencies would be a major input for investment committees we now have similarly influential ESG rating agencies. Disclosure and regulation of ESG investments by institutions is now audited. Investments that fail to score are certain threshold are explicitly excluded from receiving investment.
Your dream 19 seat TP would no longer be deemed an acceptable investment by institutions. In the current Climate (!).
You might point to the Cessna 408 and cry “nonsense” and it is true, this aircraft exists and they are a public company. However, they internally funded this TP. Textron is a publicly traded company, they will and are facing investment pressure as the Tobacco companies and others before them did.
I would point out the massive investments infantile, scaled up, toy drones have received on the basis of ESG principled investment and presented as “the socially acceptable future of air travel”.
In case you think this is hyperbole on my part, have you heard of “Ecocide”? Ecocide has not yet been accepted as an internationally punishable crime by the United Nations but successive COP’s have edged closer and closer to achieving this goal. Activities that might constitute ecocide include “substantially damaging or destroying ecosystems or by harming the health and well-being of a species, including humans.” Aviation is always pointed out as being one of these activities (that) they seek to criminalise.
But good luck with your TP anyway.
Hi Fastship,
the idea of this series is not to develop a new aircraft, on the contrary. It’s to inform the hundreds of entrepreneurs and investors of the most fantastic “a rendering and description of my pet idea” projects of the last years, what these upstarts have to go through before there can be a product that can be sold. You point to an additional hurdle on top of the technical and managerial challenges the regulations have put in place, well received.
When I learned to fly in the military the teachers told us our rulebook’s pages were all written in blood, so we better take them seriously. There is a very good reason every FAA/EASA… rule is there. It’s to avoid us being the passengers of unsafe “my pet idea” machines.
Typical elapsed time of A and C check in a major airline for a ” middle age” A320/B737 are respectively 2 and 5days.
For brand new a/c a night and 3 days. Obviously depending of your workforce in the middle of the grounding.
A week for a A check on your 19 seat a/c looks for me too long even with a single mechanics.
Question : is there an economical interest for such regional airline to subcontract such check to MRO or to hire on a temporary basis additional mechanics to speed up work even if you face “space ” restrictions on such 19 seat a/c.
It would be interesting to know figures for a Twin Otter for instance